
CSA & UL Certified Packaging Machinery
Protect Your Business with Certified Packaging Machinery
CSA and UL certifications are crucial for packaging machinery because they ensure that the equipment meets safety standards set by regulatory bodies. CSA stands for Canadian Standards Association, while UL is short for Underwriters Laboratories.
Serious Original Equipment Manufacturers (OEMs) typically have their machinery undergo rigorous testing to obtain CSA or UL Certification. Certified products help manufacturers avoid legal liabilities or fines due to non-compliance with regulations. They also play an essential role in ensuring that packaging machinery operates safely without posing any risk of harm to operators or consumers.
CSA and UL certifications clearly demonstrate an OEM’s commitment to producing products that meet international standards. Both accreditations are accepted across North America, so either one will have you covered!
Importance Certified Machinery in Manufacturing Operations
CSA and UL certifications are required by regulatory bodies such as Occupational Safety and Health Administration (OSHA) in the United States or Workplace Safety & Prevention Services (WSPS) in Canada. Having CSA/UL certified machinery can also enhance a company’s reputation among customers and stakeholders. It shows that an organization values quality control measures and prioritizes employee safety while providing reliable products/services.
Research shows that non-certified machinery has a higher likelihood of malfunctioning, which can lead to significant safety hazards for employees and could result in costly legal implications if an accident were to occur due to negligence on behalf of the company.
CSA/UL certification of industrial machinery should be a top priority for businesses looking at minimizing risks of accidents/injuries while improving their bottom line through reduced liability claims & increased productivity levels owing particularly due to reduced machine downtimes/maintenance requirements over time.
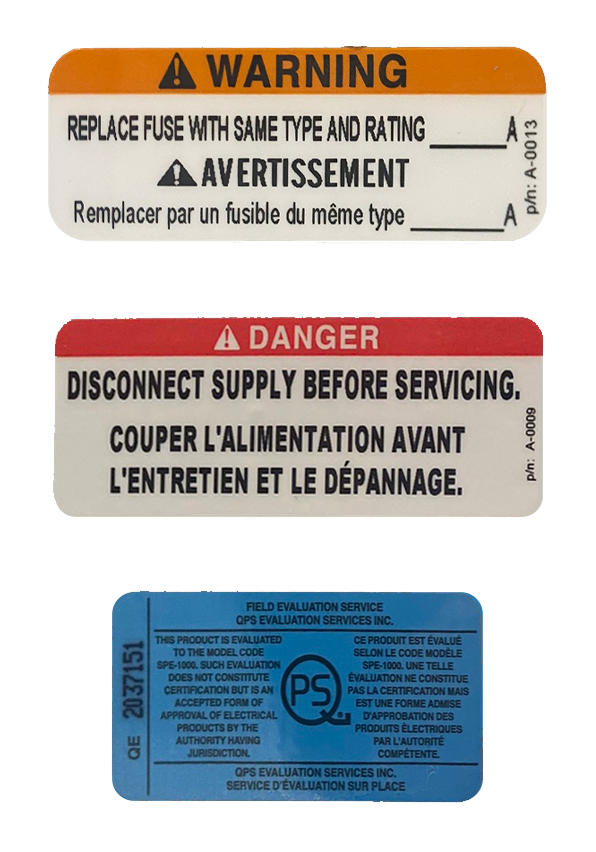
CSA & UL Certification’s Manufacturing Benefits
CSA and UL certified packaging machinery plays an essential role in helping food manufacturers ensure the safety of their workers and products. By using CSA or UL certified machines, manufacturers can comply with industry regulations and reduce the risk of worker injury and product recalls due to faulty equipment. Overall, utilizing CSA & UL Certified packaging machinery is crucial for ensuring safe manufacturing processes while maintaining customer satisfaction through consistent quality assurance practices.
Reduced Work Related Injuries
Electrical certification clearly indicates that the machinery meets the required safety standards and regulations. Using non-approved machinery may not only be illegal, but it also poses a risk to the manufacturer that has purchased the machinery & the workers operating it.
Research conducted by OSHA on injury costs related to manufacturing industries between 2011-2016; work-related injuries resulted in $59 billion worth of direct workers’ compensation costs per year for employers across all private industry sectors combined.
One of the most common worker-related injuries associated with uncertified equipment is electrical shock, which occurs due to poor insulation or faulty wiring. According to Occupational Safety and Health Administration (OSHA), electrical hazards are responsible for around 5-10% of all workplace fatalities in the United States alone.
Reduced Equipment Failure
Electrical certification applies a rigorous testing process to ensure the machinery meets high-quality standards. As a result, certified machinery tends to be more reliable and durable.
According to a study published in Food Protection Trends, “equipment failure” was one of the top three causes of foodborne illness outbreaks in North America between 2014-2018. Therefore, investing in reliable packaging machinery not only protects consumers but also helps businesses maintain their reputation and avoid costly legal consequences.
Increased Safety Measures
CSA & UL certifications evolve over time, incorporating new technologies and standards to keep up with changing industry needs. Recently CSA & UL safety certifications increased safety measures that ensure better protection against electric shock and fire hazards.
Improved Efficiency and Productivity
CSA and UL certifications ensure that packaging machines are designed to operate efficiently with minimal downtime, streamlining their production process by eliminating potential safety hazards that can cause shutdowns. The results in increased productivity and reduced production costs lead to higher profitability.
Enhanced Reputation
Manufacturers who use certified packaging machinery demonstrate their commitment to the safety of their employees and customers and the quality of their product. Their reputation is automatically improved, as is their relationships with customers and retailers.
Meeting CSA & UL Certification Standards
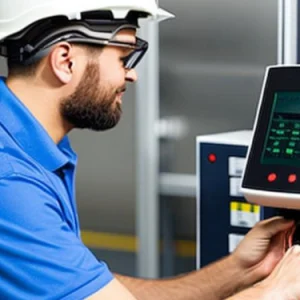
- Design Review:
Examination of the electrical system design including wiring, grounding & protection devices. - Testing and Certification:
The product must undergo a series of rigorous electrical tests - Manufacturing and Quality Control:
The OEM must have appropriate manufacturing and quality control processes in place to ensure consistent quality of the product. - Documentation:
The OEM will receive a complete and accurate certification report of the product, including specifications and test reports. - Labeling:
The product must be appropriately labeled with the appropriate CSA or UL certification mark to indicate that it meets the applicable safety standards.
All Link Pack machinery & equipment distributed through Link-Pack
is CSA or UL certified.
Regulatory Bodies Overseeing Packaging Equipment
Regulatory bodies play a crucial role in ensuring that packaging equipment meets the required safety standards. In the United States, one of the main regulatory bodies overseeing packaging equipment is the Occupational Safety and Health Administration (OSHA). OSHA sets specific guidelines for machine guarding, electrical safety, and ergonomic design to prevent accidents related to packaging machinery.
Additionally, the Food and Drug Administration (FDA) regulates machines used in food processing facilities to ensure they meet certain requirements such as sanitation and product safety. The International Organization for Standardization (ISO) also provides industry-wide regulations on quality management systems for manufacturers of packaging materials and equipment worldwide. Compliance with these regulations is not only necessary from a legal standpoint but also helps companies reduce risks associated with workplace injuries or product recalls due to faulty equipment.
Packaging Machinery Certifications in a Nutshell
Using certified machinery in business operations ensures safety, productivity and efficiency. By investing in quality equipment that meets the necessary standards, businesses can avoid costly accidents, downtime and legal issues. Furthermore, certified machinery often comes with warranties and support services that can help extend its lifespan and performance. It’s important to do your research before making any purchases or rentals. Remember: Safety starts with choosing the right tools for the job!
Other Blogs of Interest
ShurTAPE’s rPET Tapes – Boost Packaging Efficiency and Sustainability in Quebec
Discover the benefits of flexible pouches for liquid packaging and how they can transform ...
Liquid Pouch Packaging Solutions – A Guide to Flexible Packaging for Liquids
Discover the benefits of flexible pouches for liquid packaging and how they can transform ...
Essential Maintenance Tips for Your Filling Machine
Follow these maintenance tips to maintain your automatic or semi-automatic filling machine...
CSA & UL Certified Packaging Machinery
You can't go wrong with CSA or UL certified packaging machinery. Uncertified equipment may...
The Value Behind TCO
How can the Total Cost of Ownership (TCO) help your approach and enhance the approval for ...
Packaging Machinery and Integration
Packaging machinery integration involves methodical planning to combine packaging equipmen...