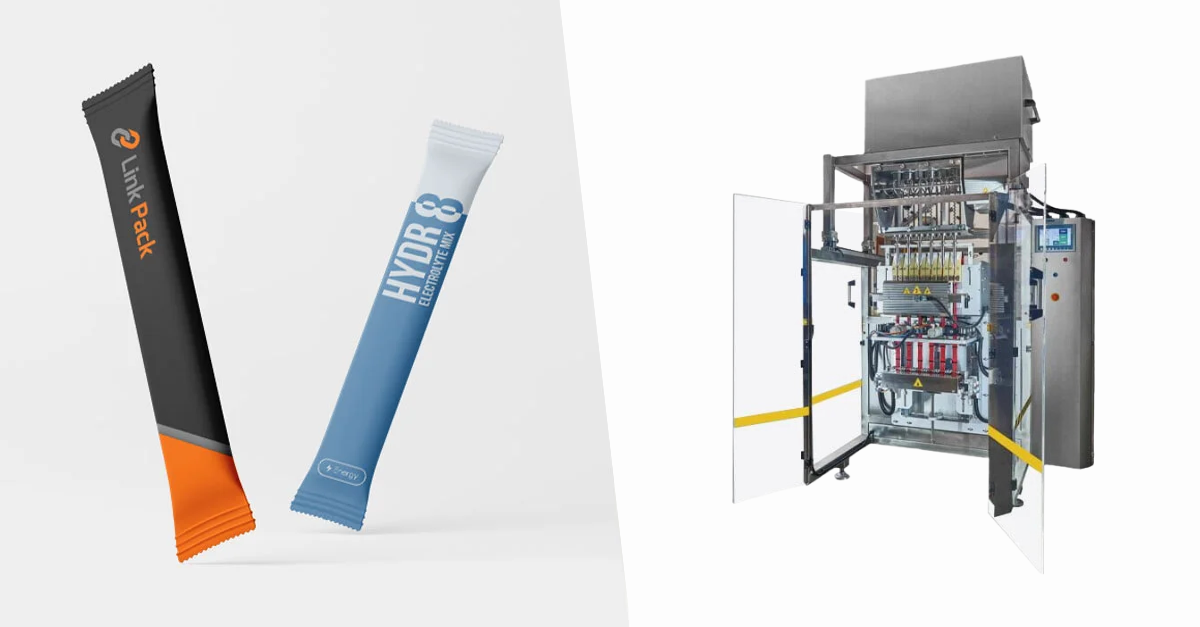
Stick Pack Machines – Process & Operation
Stick Pack machines are revolutionizing the packaging of supplements, nutraceuticals, and pharmaceuticals, offering efficiency and versatility. Let’s explore how this advanced machine converts a single roll of laminated film into the convenient stick packs that consumers love.
Why Choose Stick Pack Format?
Stick packs are gaining popularity across various industries due to their portability, convenience, and ease of use. Manufacturers appreciate the high throughput and space-saving benefits of stick pack machines like the Mentpack 101-S, which can produce up to 1,200 stick packs per minute. Operating a stick pack machine is very similar to a VFFS single-lane vertical form-fill-seal packaging machine, but can reach up to 24 lanes forming sachets simultaneously. Barrier film is unwound and travels through the machine vertically into the lanes where the film is formed and filled with powdered, granular, liquid, viscous or gel products.
The stick pack format, also known as the single-serve format, is gaining popularity among consumers due to its portability, convenience, and ease of use. Manufacturers and co-packers favor stick-pack machines because they can achieve high throughputs and save valuable plant floor space. Continue reading for more details on how vertical stick pack machines work.
How Do Stick Pack Machines Work?
Film Transport & Unwind
The process begins with a roll of film, or roll stock, positioned at the machine’s rear. The film unwinds and a single sheet is fed into the machine using a pneumatic shaft. The cross-seal jaws at the front handle the unwinding, with photocells ensuring proper alignment. This precise control guarantees that the film is always positioned correctly for the subsequent steps.
Optional Printing Features
For variable information printing, the machine is equipped with a coder. The film passes over a registration roller, aligning the date stamp with the horizontal seal. The machine can incorporate laser, thermal, inkjet, or thermal transfer printers based on customer requirements, ensuring flexibility in printing solutions.
Maintaining Film Tension
Dancer arm controls are crucial for maintaining consistent film tension. These arms, equipped with rollers, move to keep the film under tension as it is transported, preventing it from wandering side to side.
Precision Film Cutting
The film then moves into the cutting section. The Mentpack 101-S features motorized cutting disk knives, which ensure precise cuts. The motorized cutters help maintain film tension, resulting in high-quality stick packs.
Efficient Stick Pack Discharge
After filling, the packs are cut or notched below the horizontal seal jaw, ready for secondary packaging. There are also various discharge solutions tailored to different secondary packaging needs.
Filling and Sealing Stick Packs
Once the film stops moving, vertical seal bars create the vertical seal. A horizontal sealing jaw then seals the top of one stick pack and the bottom of the next. The product is filled into each stick pack with great accuracy using volumetric fillers, liquid pumps, or auger fillers and servo motor systems ensure contamination-free sealing, even for liquid products.
Efficient Stick Pack Discharge
After filling, the packs are cut or notched below the horizontal seal jaw, ready for secondary packaging. There are also various discharge solutions tailored to different secondary packaging needs.
Efficient Stick Pack Packaging with the Mentpack 101-S
Innovative Stick Pack Auger Filler by Mentpack
The latest design in stick pack auger fillers from Mentpack includes several groundbreaking features.