
Automation and Plastic Container Packaging
Plastic Container Packaging Machines
When we say plastic container packaging machine, we refer mainly to the automation solutions for packaging consumer products into rigid plastic bottles, cups, tubs, and pails. Rigid container machinery is a broad category encompassing an array of modern machinery with many valuable attributes for consumer goods industries. Automation leads to increased productivity, improved product quality, heightened worker safety, and reduced factory lead times. Human artistry is still highly prized in some sectors, but there is no comparison to the greater quality control and product consistency attributable to automated processes.
So what systems are necessary for the full automation of plastic container packaging, and will the use of plastics remain popular in the face of growing concerns for sustainability? Our guess is that some form of rigid “plastic” packaging will remain among the favorites in many industries, though the materials used to fabricate them will evolve into something we can all stand behind as manufacturers and consumers. But only the future will tell when it actually comes to fruition.

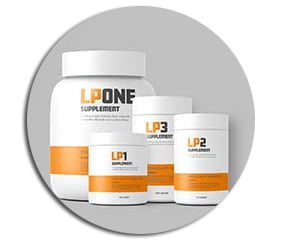
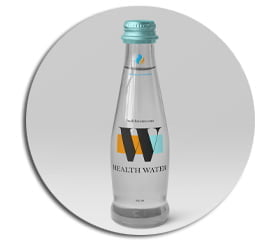
4 Main Plastic Container Packaging Machine Categories:
Weighing, Filling & Depositing
In these systems, sensors provide more accurate masses of product following a predetermined process. The weighed amount is released into a depositing system depending on the product type. Auger fillers are often used for powders, multi-head weighers are mostly used for granular materials, and volumetric or piston fillers are more common for liquids.
Sealing
Heat sealing plastic containers and locks in freshness, prevent leaks, and preserve freshness with hermetic seals for packagers of food, beverage, pharmaceuticals, health & beauty products, and chemicals.
Lidding, Capping & Closing
Automated Lidding, capping & Closing machinery is available for all kinds of open-mouth container shapes and sizes. Some solutions are custom-made to include denesters, lid sorters, and lid depositors, enhancing throughput.
Labeling
Plastic containers almost all use some form of labeling whether it be front & back, top & bottom, wrap, tamper evident or a mix of the afore mentioned. Automated labeling machines are found in linear formats for lower production volumes and rotary labeling machinery is highly effective for larger volumes.Both can be outfitted with multiple labeling applicators to include all necessary packaging branding, regulatory information, and options tailored for plastic container packaging.
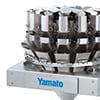
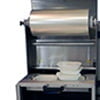
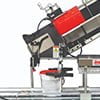
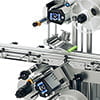
Plastic Container Packaging
Plastic containers remain one of the preferred materials for the food and beverage industry mainly due to the benefits attributed to their lightweight and preservation of the packaged product and because they hold their shape and stand upright. One of the biggest advantages of rigid packaging is that products are delivered exactly as intended.
Luckily, fossil-fuel-derived plastics are becoming less popular. PET is now extensively used for various applications and is completely recyclable. It has quickly become the most recycled plastic worldwide.
We are seeing an increasing number of materials tested to improve the sustainability of plastic container packaging solutions. Some breakthroughs have come to the surface during the pandemic, notably paper bottles. This exciting breakthrough produces sustainable bottles that are biodegradable and working their way to being completely compostable. There is also extensive ongoing research into cellulosic materials used for rigid containers because it is the most naturally occurring resource on earth.
Most industries are pushing for greener alternatives because consumers now are more inclined than ever to prefer eco-friendly products and drop plastic packaged products like they are hot.
Switching to Greener Plastic Container Packaging
Adapting your product packaging to meet sustainability is commendable; that being said, it is vital to work closely with your OEM to test new materials. You may need to work through modifications to account for filling allowances, melting points, line speed, and even labeling efficiency. Before changing your product packaging, checking with your equipment manufacturer will always be your best bet.