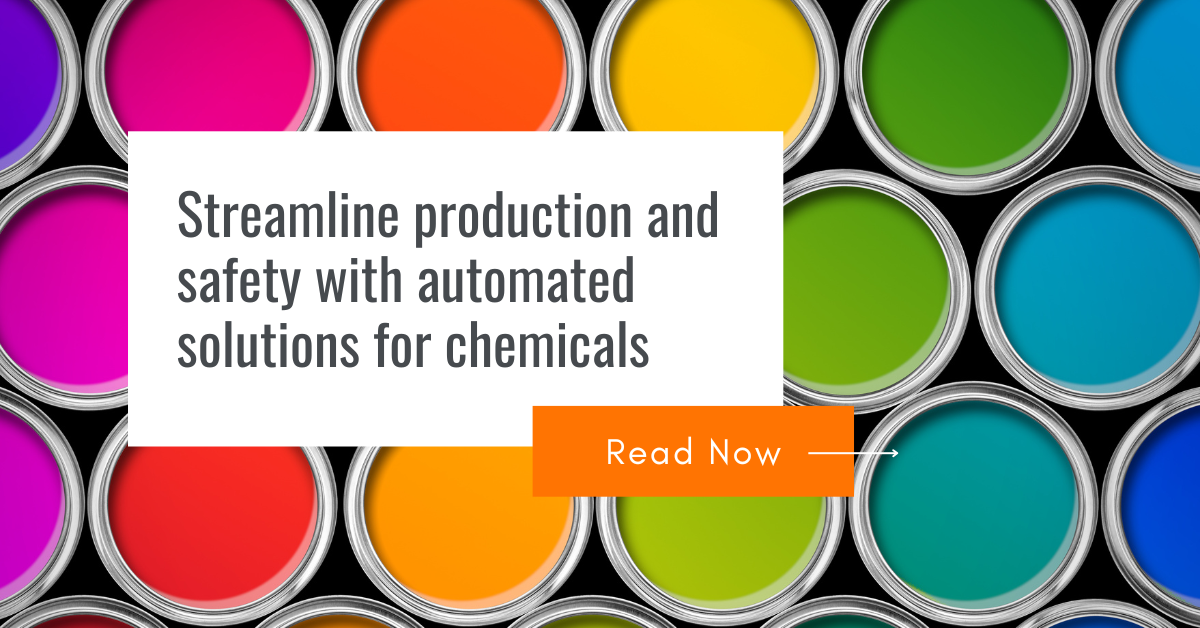
Automated Packaging Solutions Tailored for Chemicals and Coatings
Streamlining Chemicals & Coatings Industry Production:
How Automated Packaging Machinery Solves Key Pain Points
Adaptability plays a crucial role in chemical manufacturing. Whether you’re producing paints, thinners, adhesives, or industrial coatings, your operation likely juggles a wide range of products with varying viscosities, container sizes, and labeling requirements. Product diversity creates unique challenges that can slow down production, increase costs, and compromise quality if not addressed effectively. However, while this diversity presents challenges, it also opens doors for improvement and innovation. Let’s explore the most common challenges faced by chemical manufacturers and how automated filling and labeling machines can transform the game by streamlining processes, enhancing efficiency, and maintaining high-quality standards.

Automation in Chemicals & Coatings is Trending
Did you know that the chemicals and coatings industries are making a decisive shift toward automation to stay competitive? According to a 2023 report by PMMI (The Association for Packaging and Processing Technologies) , over 65% of chemical manufacturers have invested in automated packaging solutions in the past two years alone. Why? Because automation doesn’t just streamline operations—it also drives efficiency, reduces waste, and ensures compliance with increasingly strict regulations.
Consider these facts:
- A study by McKinsey & Company found that companies implementing automation in their packaging lines saw a 20-30% increase in productivity.
- The American Coatings Association (ACA) reports that businesses using automated systems reduced material waste by up to 15% , saving both money and resources.
These numbers speak for themselves. If you’re still relying on outdated manual processes, now’s the time to consider upgrading to automated solutions. Not sure where to start? Keep reading, we’ll walk you through the top pain points and what machinery can help solve them.
Pain Points Faced in the Chemicals & Coatings Industry
Handling Diverse Products and Viscosities
Chemical and coatings manufacturers often produce a variety of products, from low-viscosity liquids (like thinners) to thick, paste-like substances (such as epoxy resins). Traditional packaging equipment struggles to adapt to such variability, leading to inefficiencies and inconsistent results.
- Pain Point : Manual adjustments for different products waste time and increase the risk of errors.
- Impact : Inconsistent fills can lead to customer dissatisfaction, product recalls, and wasted materials.
Meeting Strict Regulatory Requirements
The chemicals and coatings industry is heavily regulated, with stringent labeling standards like GHS (Globally Harmonized System) compliance. Non-compliance can result in hefty fines, legal issues, and reputational damage.
- Pain Point : Ensuring every label meets exact specifications while maintaining high throughput.
- Impact : Manual labeling processes are prone to human error, making it difficult to stay compliant.
Scaling Production Without Compromising Quality
As demand grows, manufacturers need equipment that can scale efficiently without sacrificing precision or speed.
- Pain Point : Manual operations and outdated machinery may bottleneck production during peak seasons.
- Impact : Missed deadlines, lost revenue, and strained relationships with distributors.
ATEX Compliance and Anti-Explosion Machine Configuration
Many chemicals and coatings, such as solvents, thinners, and adhesives, are highly flammable or volatile, posing significant risks in production environments. To mitigate these dangers, manufacturers can invest in equipment that complies with ATEX (ATmosphères EXplosibles) standards or equivalent anti-explosion regulations.
- Pain Point : Increased risk of fires, explosions, and workplace accidents which sometimes result in costly fines, legal liabilities, and reputational damage.
- Impact : Operational disruptions due to safety incidents, increased insurance premiums, and potential shutdowns by regulatory bodies.
Minimizing Waste and Maximizing Sustainability
With rising environmental concerns, manufacturers face pressure to reduce material waste and adopt eco-friendly practices.
- Pain Point : Overfills, spills, and misaligned labels contribute to unnecessary waste.
- Impact : Increased costs and negative environmental impact harm both profitability and brand reputation.
Solve Packaging Challenges with Machinery
Flexible Filling Solutions for Diverse Products
When it comes to handling a variety of viscosities, Serac’s filling machines stand out as trailblazers in filling machinery. Their expertise allows them to tackle pain points faced by industrial coatings suppliers. Serac offers versatile systems, with filling nozzles capable of adapting to both free-flowing liquids and highly viscous materials.
- How It Works : Serac’s volumetric piston fillers use precision-engineered components to deliver consistent fills regardless of viscosity. Their modular design allows quick changeovers between products, reducing downtime and boosting productivity.
- Real-World Benefit : For example, a manufacturer producing both lacquers and sealants can switch between formulations seamlessly, ensuring accuracy within ±0.5%. This level of flexibility is critical for businesses managing diverse product lines.
Precision Labeling for Compliance and Branding
Accurate labeling is non-negotiable in the chemicals and coatings industry, where regulatory compliance and branding go hand-in-hand. Manual labeling processes are prone to human error, which can lead to costly mistakes, such as misaligned labels, incorrect information, or non-compliance with GHS (Globally Harmonized System) standards. Automated labeling systems, like Link Pack’s linear wrap labelers and Gernep’s rotary labelers, eliminate these issues by delivering consistent, precise results every time.
- How It Works : Link Pack’s wrap labelers can be customized with vision technologies or simple prism aligners to orient containers then apply labels smoothly around cylindrical containers, even labels with bail perforation. Meanwhile, Gernep’s rotary labelers excel at applying front, back, and wrap-around labels with pinpoint accuracy at high speed. Both OEMs can integrate optional vision inspection units to validate information printed on the label, label presence, and more.
- Real-World Benefit : According to a 2021 study published in the Journal of Manufacturing Systems, automated labeling systems reduce labeling errors by up to 95% compared to manual processes. The study analyzed data from over 50 manufacturing facilities and found that automation not only improved accuracy but also increased throughput by 30-40%.
Ensuring Safety in Hazardous Environments with ATEX-Compliant Equipment
Chemical manufacturers often handle volatile substances like solvents, thinners, and adhesives, which pose significant safety risks if not managed properly. Packaging machinery can be designed to operate safely in potentially explosive atmospheres, ensuring both worker safety and uninterrupted production.
- How It Works : Serac’s filling machines are engineered to meet ATEX specifications, a European directive governing equipment used in explosive environments. These machines incorporate explosion-proof components, anti-static materials, and fully enclosed designs to prevent ignition hazards.
- Real-World Benefit : According to a 2023 report by the Occupational Safety and Health Administration (OSHA) , facilities using explosion-proof equipment reduced incidents related to fires and explosions by up to 45% . This underscores the importance of investing in certified machinery to mitigate risks.
Eco-Friendly Operations Through Automation
Reducing waste isn’t just good for the planet—it’s also great for your bottom line. Automated systems minimize overfills, spills, and misalignments, contributing to more sustainable operations.
- How It Works : Serac’s precision fillers reduce material waste by up to 20% , while Link Pack’s labelers eliminate rework caused by misapplied labels. Together, these technologies help manufacturers achieve leaner, greener workflows.
- Real-World Benefit : A study by PMMI found that companies adopting automated packaging solutions reduced material waste by an average of 15% , translating to significant cost savings and improved sustainability metrics.
Scalable Equipment for Growing Demand
As your business expands, so does the need for scalable equipment. Gernep offers what they call pre-modular designs that grow with your operation.
- How It Works : Gernep rotary labelers can be designed with expansion in mind – with frames allowing for additional stations to accommodate higher volumes.
- Real-World Benefit : According to a 2022 report by PMMI (The Association for Packaging and Processing Technologies) Modular designs allow businesses to scale production incrementally, avoiding the high costs associated with overhauling entire lines.
Why Invest in Automated Packaging Machinery?
By investing in automated fillers and wrap labelers, chemical manufacturers solve immediate pain points.
- Boost Efficiency : Streamline production with faster cycle times and fewer interruptions.
- Enhance Quality : Deliver precise, consistent results that meet customer expectations.
- Stay Competitive : Adapt quickly to market trends and regulatory changes.
- Future-Proof Your Business : Scale effortlessly as demand grows.
Ready to Transform Your Packaging Process?
If you’re ready to propel your chemical or coatings manufacturing, we’re here to help. Our team specializes in connecting businesses with the right automated packaging solutions tailored to their unique needs.
- Need a flexible filler? Explore Serac’s innovative systems .
- Looking for precision labeling? Check out Link Pack’s labelers or Gernep’s rotary labelers .
- Not sure where to start? Speak with our team today to get personalized recommendations.
Don’t let outdated processes hold you back! Automate your packaging line and unlock new levels of efficiency, compliance, and sustainability.